Application Processes, Industrial
In-line Filters for Cold Adhesive Pumps & Applicators
Most industrial adhesive pumps are very robust, require little maintenance and will continue to run even if a drum has not been set up correctly. Faulty drum changes can lead to external leakage, shown below but it can also allow debris or cured material to be pumped downstream into the application equipment.
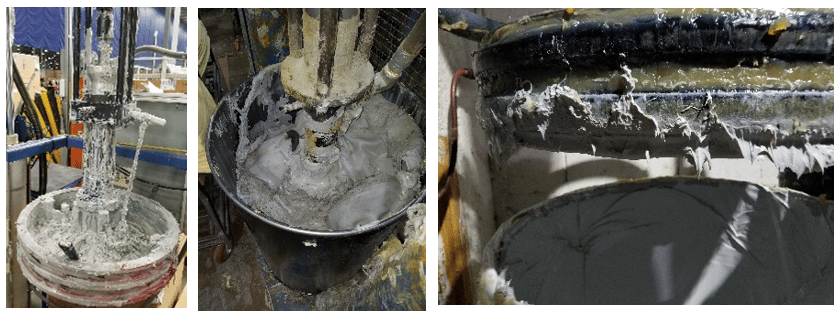
When debris or chunks of cured adhesive reach application equipment, it is not always obvious what the issue is and it can require extensive maintenance time to disassemble and remove the clog. In this post, we will outline how our in-line filtering system can prevent debris and chunks of cured material from reaching your application equipment to reduce damage, maintenance costs and increase uptime.
In-line Basket Filters
In-line basket filters can be configured to optimize the flow of adhesive while eliminating debris that exceeds the narrowest size of a given dispensing system. Selecting the best screen configuration requires evaluating the needs of the dispensing system as well as the expected pressure of the system and the flow of adhesive.
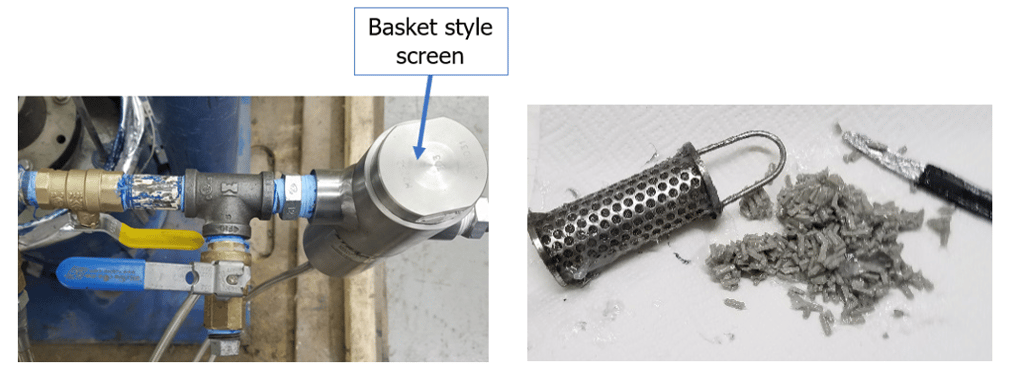
We recommend utilizing a dual-screen system so that the material flow can be diverted when one of the filter baskets is restricting flow which also allows for backflushing the loaded screens. It is also possible to run with one in-line filter and simply swap out baskets when there is a restriction.
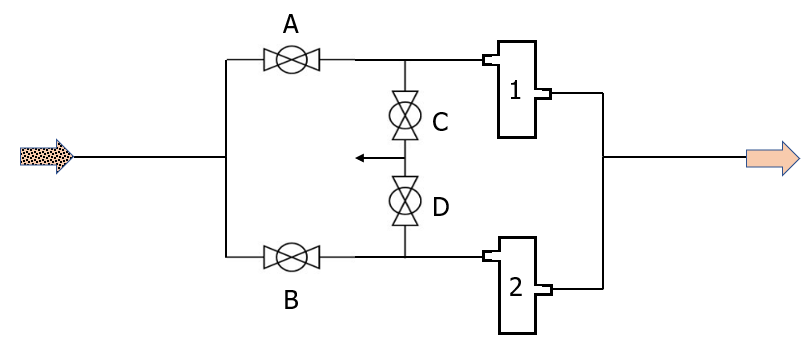
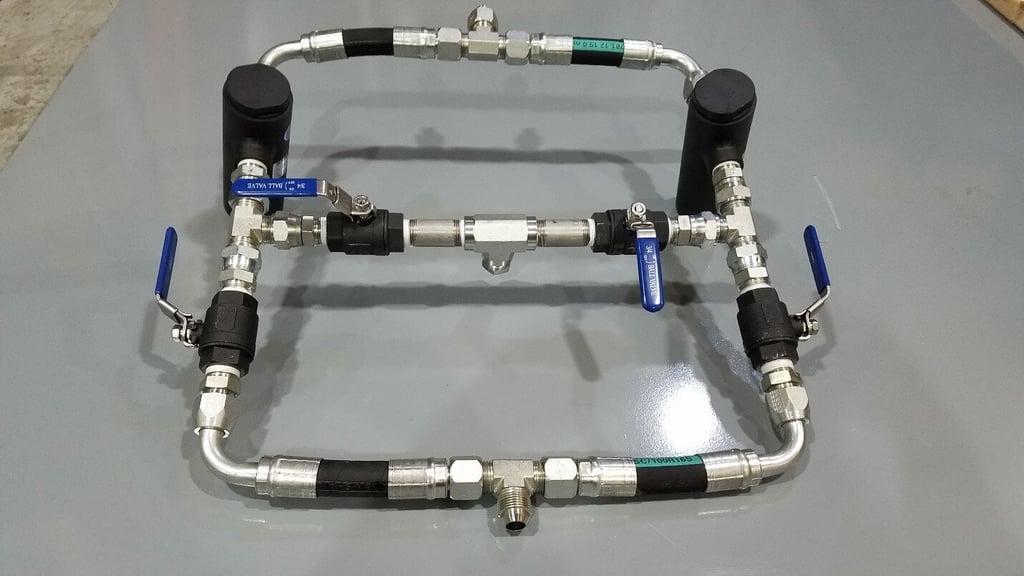
Demonstrating Effectiveness
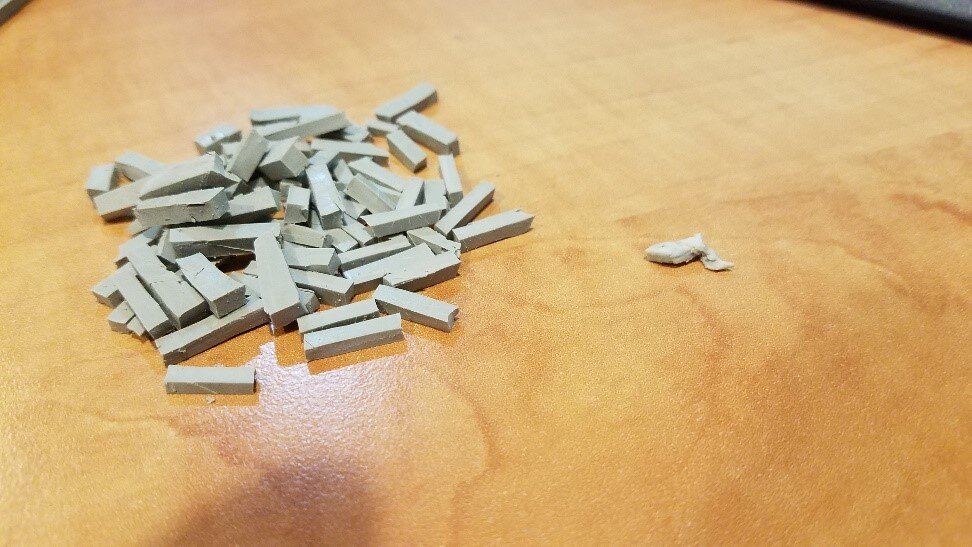
In the right side of this image is a piece of debris that was collected during the maintenance of a dispensing gun. This piece of cured adhesive is ~ 1 cm long.
In the left of the image are pieces of cured material that were cut from a sheet to represent debris for a controlled demonstration.
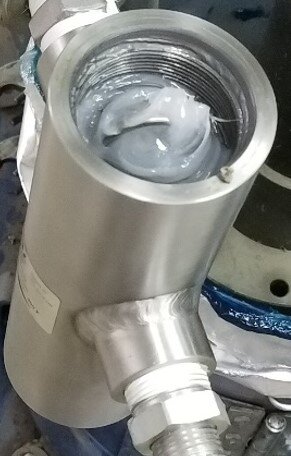
~ 6 oz. of this debris was mixed into a 5-gallon pail of clear industrial adhesive so that the effectiveness of the screen could be directly observed.
For the initial demonstration, the control debris was run through the screen with a clear, un-catalyzed industrial adhesive… allowing us to open the cartridge and see the collection of debris without risk of initiating cure inside the system. In a production environment, we would not want to expose a moisture cure adhesive to air for any significant amount of time, as it will begin to harden and cure.
When the basket is removed, you can see the debris has collected along the walls of the basket. This debris had reach ~75% of the volume of the basket, and material had continued to flow through the screen.
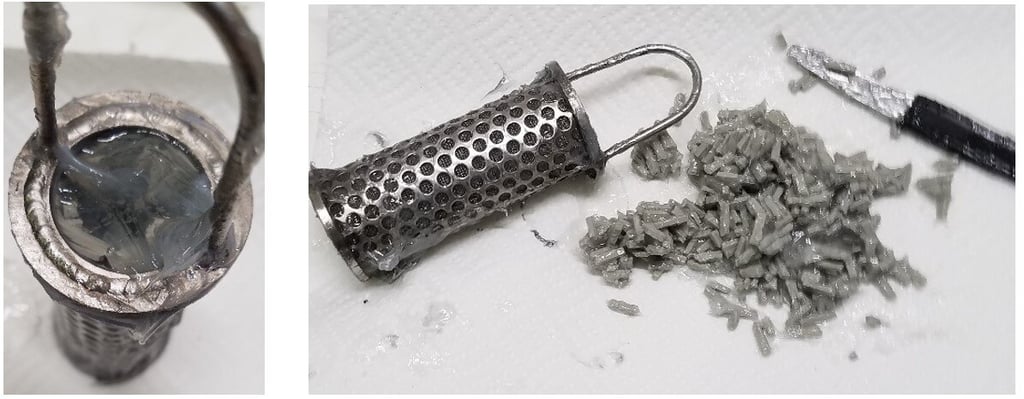
The clear adhesive was observed and collected to ensure no debris had passed through the screen.
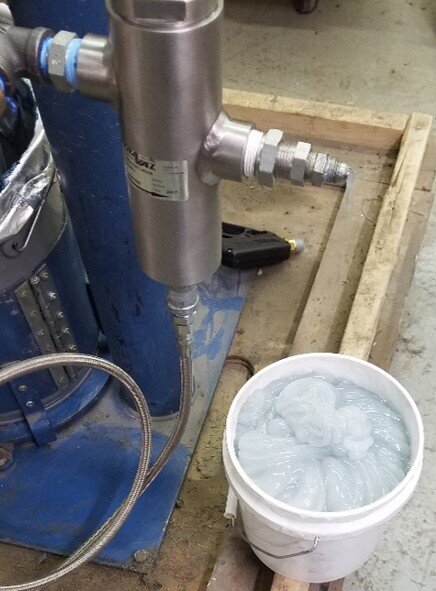
In a secondary demonstration, the debris was collected, then the adhesive was fed back through the screen and dispensed from the port shown below. The debris flushed quickly, with the majority of the particles being expelled within the first few seconds of flow.
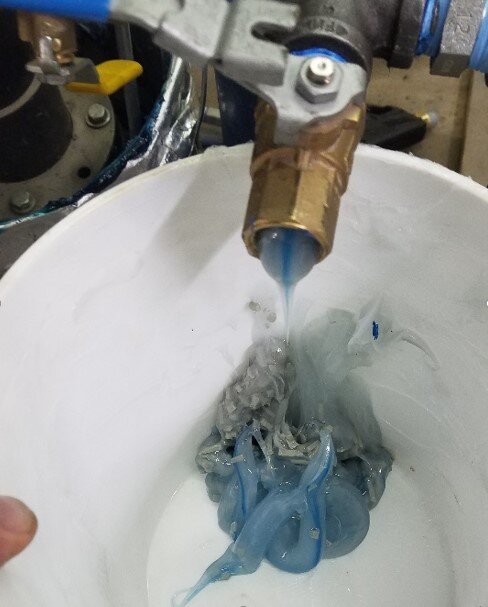
In this demonstration, there was a single screen, and so the flushing material was not screened. For a production environment, it would not be desirable to flush a screen with material that could potentially contain additional debris, and a dual-screen system protects against this.
Contact us today to discuss your cold adhesive application requirements.
Recent Posts
Archives
- August 2024 (3)
- September 2024 (3)
- October 2024 (3)
- November 2024 (3)
- January 2019 (2)
- January 2025 (2)
- March 2025 (2)
- May 2025 (2)
- October 2015 (1)
- February 2019 (1)
- March 2019 (1)
- April 2019 (1)
- May 2019 (1)
- June 2019 (1)
- July 2019 (1)
- August 2019 (1)
- November 2019 (1)
- December 2024 (1)
- February 2025 (1)
- April 2025 (1)
- June 2025 (1)